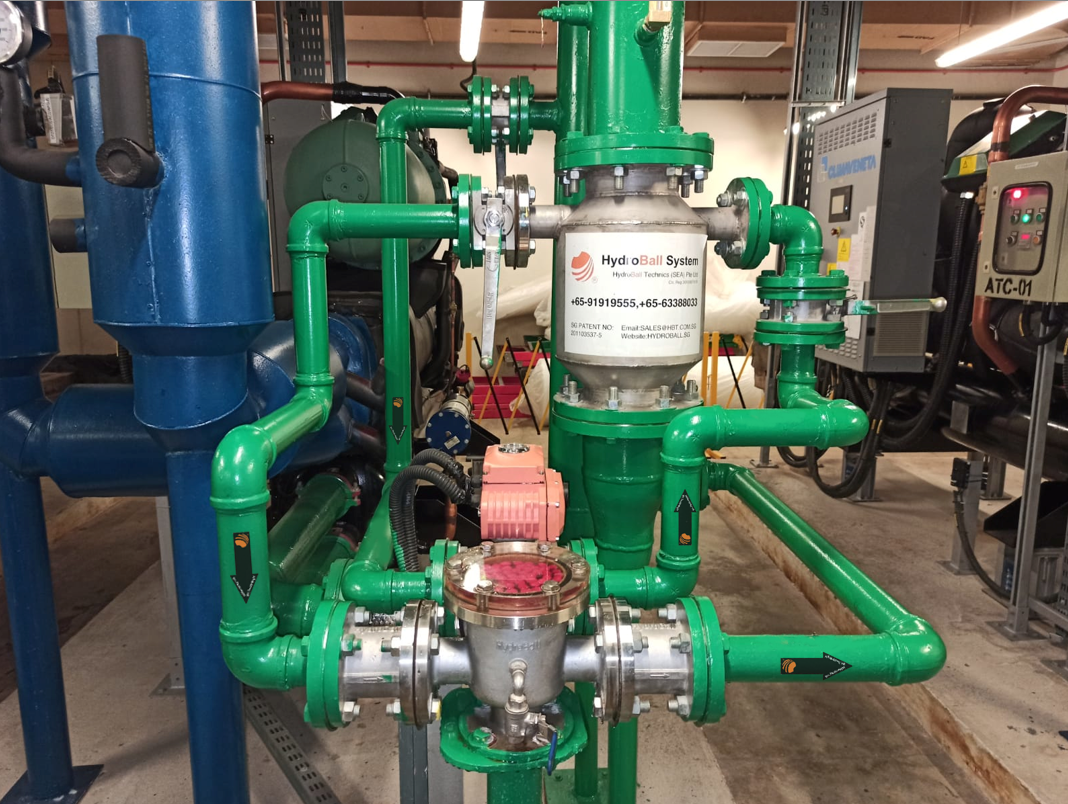
Hydroball Technics Targets 1% Reduction in Greenhouse Gas Emissions
Power generation is a significant contributor to Singapore’s carbon emissions, constituting approximately 40% of its total emissions. In line with the country’s goal of zero net emission by 2050, Hydroball Technics has been aiming to make a substantial impact by targeting a 1% reduction in greenhouse gas emissions. This effort is set to translate to a remarkable 258,800 metric tons reduction in greenhouse gas emissions, contributing to the national objective of fighting climate change.
To put this reduction into perspective, consider that in the United States, 1,402,438 kWh of electricity generation produces 576 metric tons of CO2 emissions. Therefore, Hydroball Technics’ goal of reducing emissions would result in energy savings equivalent to 630,123,185 kWh, contributing significantly to a greener and more sustainable future.
Leading the Charge Towards Sustainable Solutions With HydroBall ATC System
The company’s greatest achievement lies in the HydroBall System, a “Non-Powered” automatic tube cleaning (ATC) system launched in 2005. This innovative system addresses the challenges faced by water-cooled condenser systems within chiller plant rooms of various commercial and industrial buildings. Specialising in energy and water consumption reduction and cost efficiency, the HydroBall System has become a key component in businesses’ efforts to contribute to Singapore’s overarching goal of becoming a sustainable and environmentally responsible nation.
Three key features contributing to the success of this innovative system are:
- “Non-Powered” system which eliminates the need for prime movers like pumps, compressors, or diverters, thereby reducing maintenance requirements;
- “Water Resilience” mechanism which promotes water recycling, reuse, and circularity during regular operations, thus minimising water wastage;
- “Dual-Loop” design which prevents the re-entry of mixed hot and cold water into the condenser, thereby preserving chiller efficiency, unlike other tube cleaning systems.
They underscore the system’s commitment not only to operational efficiency but also to environmental sustainability. By preserving chemically treated cooling water, the HydroBall System actively contributes to the support of biodiversity. This approach aligns with the broader goal of mitigating the impacts of climate change, as responsible water management plays a crucial role in addressing environmental challenges.
This sustainable ACMV equipment has received the prestigious 4-tick score which is the maximum rating, under the Green Building Product Certification Scheme by the Singapore Green Building Council (SGBC) with certification numbers SGBP 4114 and 3745. It is a recognition that underscores Hydroball Technics’ commitment to providing environmentally friendly solutions for the HVAC/ACMV industry, further solidifying HydroBall Technic’s position as a leader in the green energy & water conservation space.
With the HydroBall ATC System installed, buildings can enjoy significant optimisation on energy consumption. The chiller-specific electricity consumption can be reduced by 18.4%, as supported by an independent assessment report for the HydroBall ATC System from a field-testing project funded by The Enterprise Challenge Unit (TEC Reference No: L00279/772). This substantial reduction in electricity usage not only addresses critical factors such as cooling system inefficiencies and rising electricity rates but also aligns with the company’s vision of creating a more sustainable and energy-efficient future for businesses across various sectors. Moreover, the HydroBall ATC System can lead to substantial cost savings of up to 35% on energy, water, labour and other expenses for buildings and large processing.
“As a company deeply committed to green energy & water conservation, Hydroball Technics is proud to play an important role in assisting Singapore in achieving its zero net emission target by 2050. Our HydroBall Auto Tube Cleaning System stands as a testament to our dedication to environmental sustainability, providing businesses with an effective and certified solution to reduce energy and water consumption and costs,” said Mr Peter Soh, CEO at Hydroball Technics.
Singapore is committed to peaking emissions before 2030, and achieving net zero by 2050. We have taken concrete steps to reduce our carbon footprint. These include gradually increasing our carbon tax rate, facilitating renewable energy imports and promoting energy efficiency. Everyone needs to fight climate change – the Government, businesses, and households.
“In 2019, to optimise energy consumption at the systems-level, we introduced Minimum Energy Efficiency Standards (MEES) for water-cooled chilled water systems to encourage the adoption of energy-efficient chilled water operations by industrial facilities.
Mandatory MEES requirements were introduced for new industrial facilities in 2020. This has helped new facilities each save an average of $300,000 annually in electricity costs, recouping their initial outlay just after 3 years.
We will amend the Energy Conservation Act this year to effect similar requirements for existing industrial facilities from December 2025. Existing industrial facilities can expect average energy savings of about S$1.25 million per year per facility across the system’s 15-year lifespan, and to recover retrofitting and operating costs within 5.5 years.” said Dr Amy Khor, Senior Minister of State for Sustainability and the Environment.